LFT Model with Pre-Shrink Handle Applicator
Single and double track
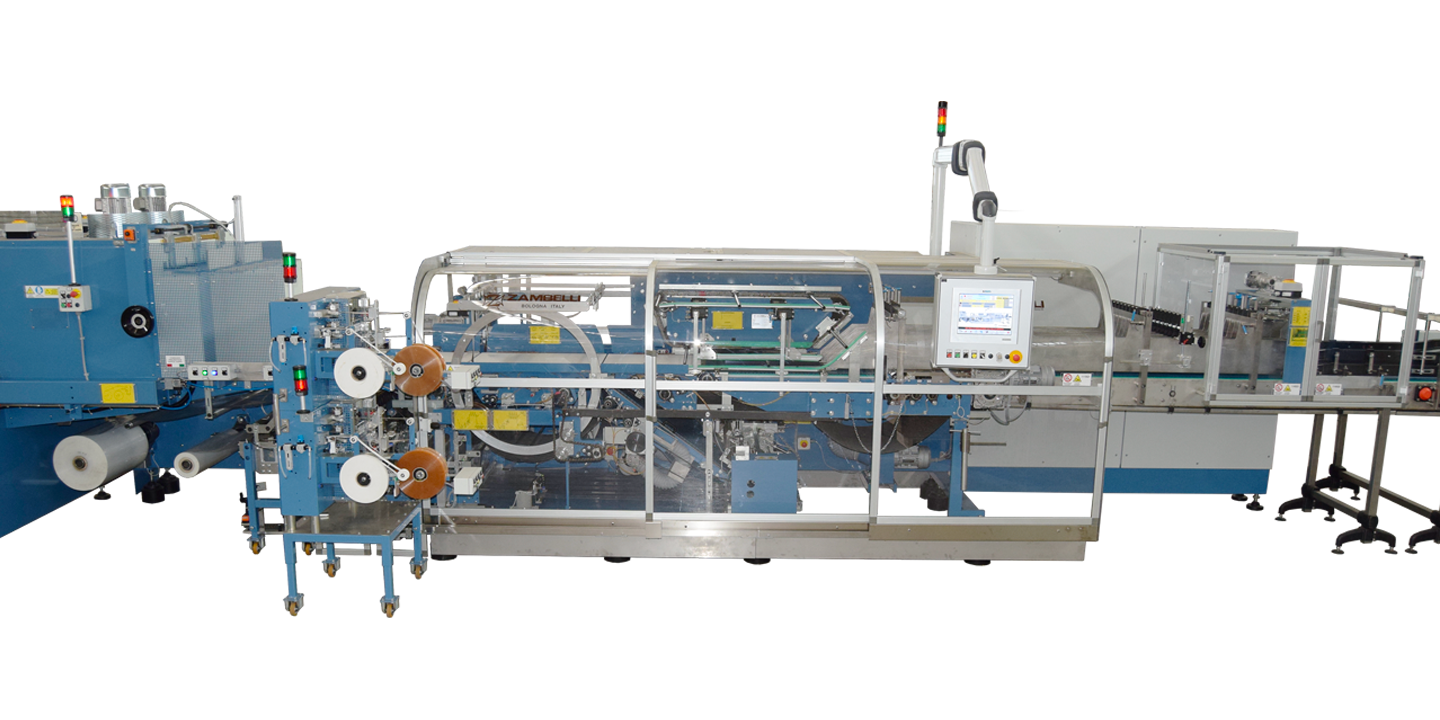
Details
The LFT model with pre-shrink handle applicator is a shrink wrap machine available in single and double lane versions.
The applied handles are resistant and comfortable for transport by the final consumer.
Energy saving tunnel
The shrink tunnel present in all Zambelli Shrink wrap machines has 7 fundamental characteristics:
- Tunnel flow setting through adjustable holes
- Extra resistors already installed (zero downtime replacement)
- Minimum energy consumption
- Three possible configurations on the same tunnel (1, 2 or 3 lanes)
- Separate cooling section at the exit for best shrink
- Tunnel adjustment according to the film characteristics
- Possibility of working with different types of films by adjusting the air flows and temperature
Machine Details
Special groups
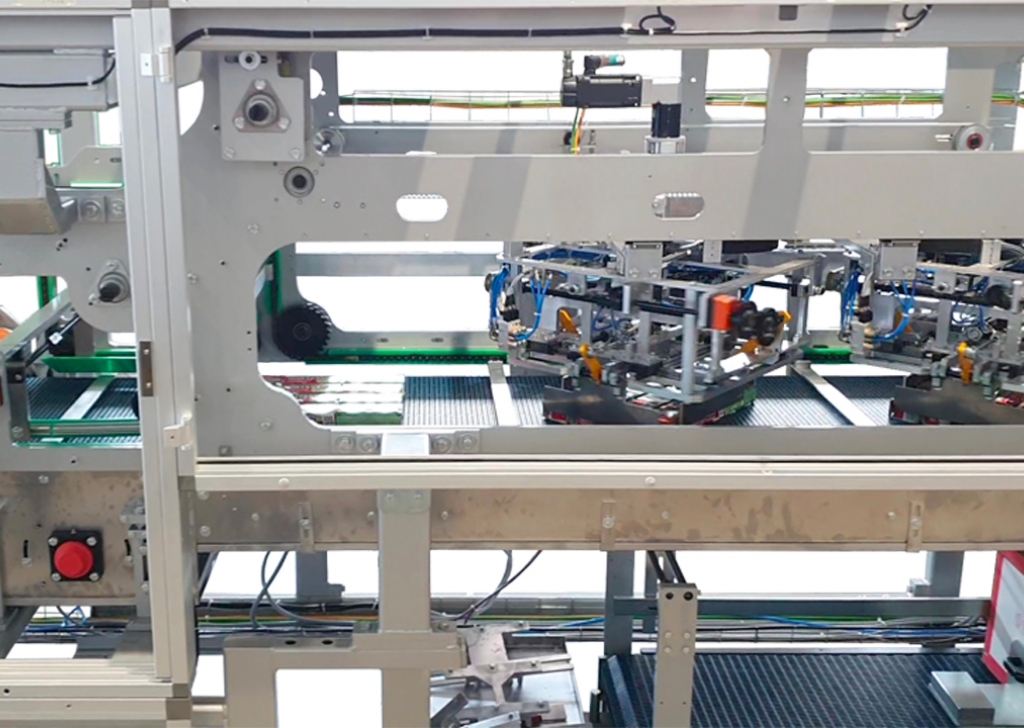

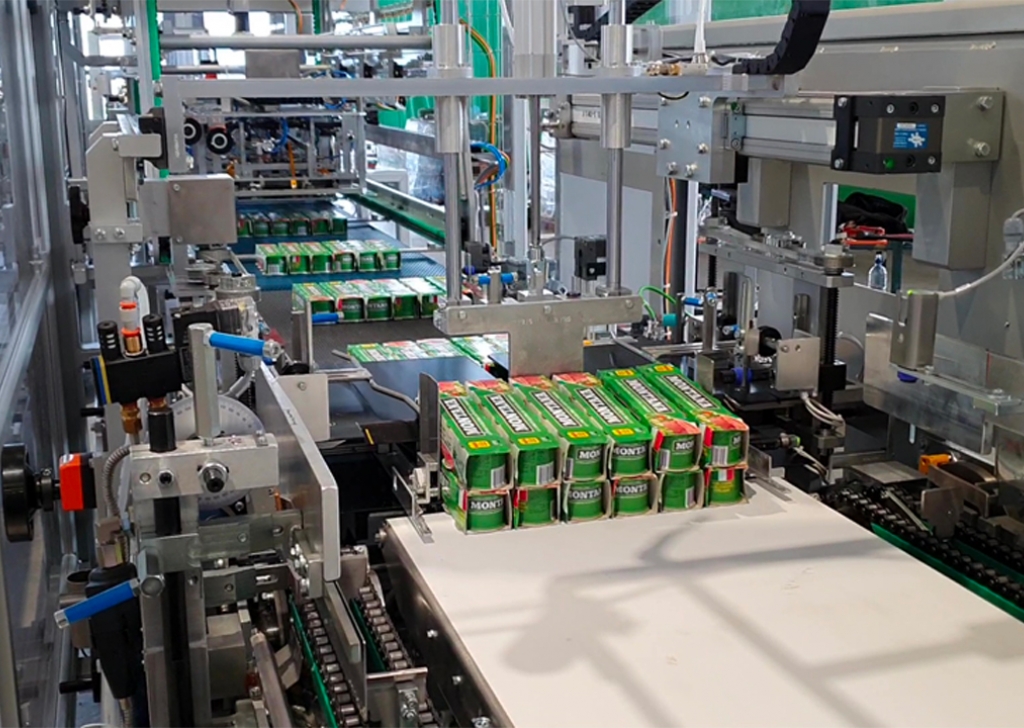
A conveyor with intermittent vertical movement deposits a layer on the upper surface. The upper surface is adjustable by means of a handwheel with numerical indicator based on the height of the cluster.
Subsequently a motorized trolley accompanies the product step by step with the tray formation group or on a belt to create a bundle in film only or flat pad.
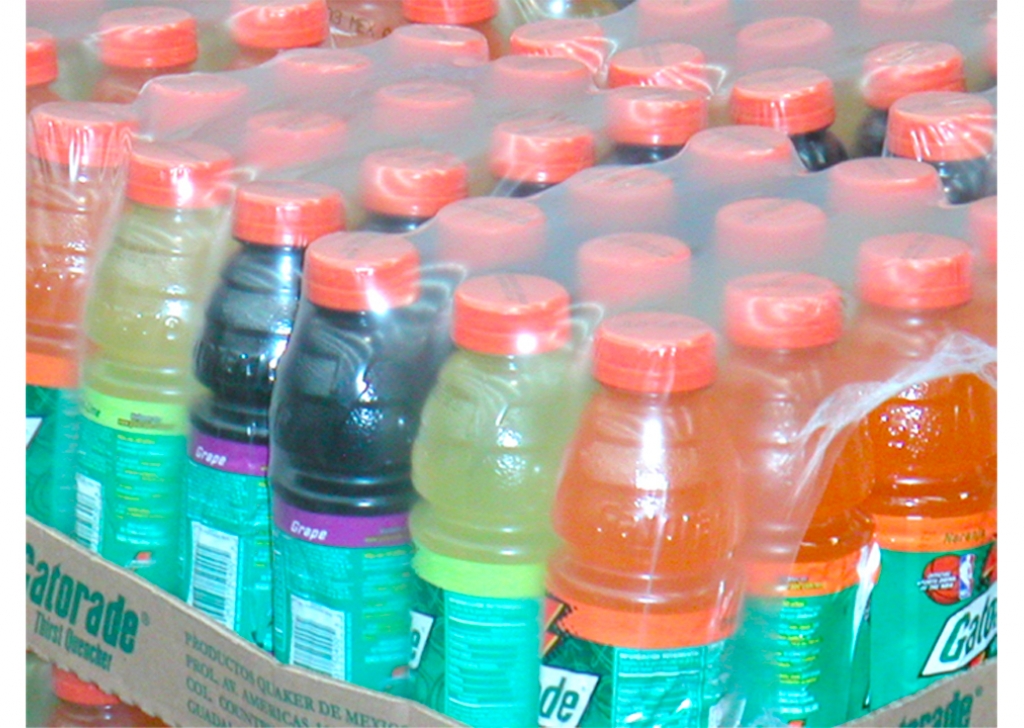
It can be built in line or with rotary tables.
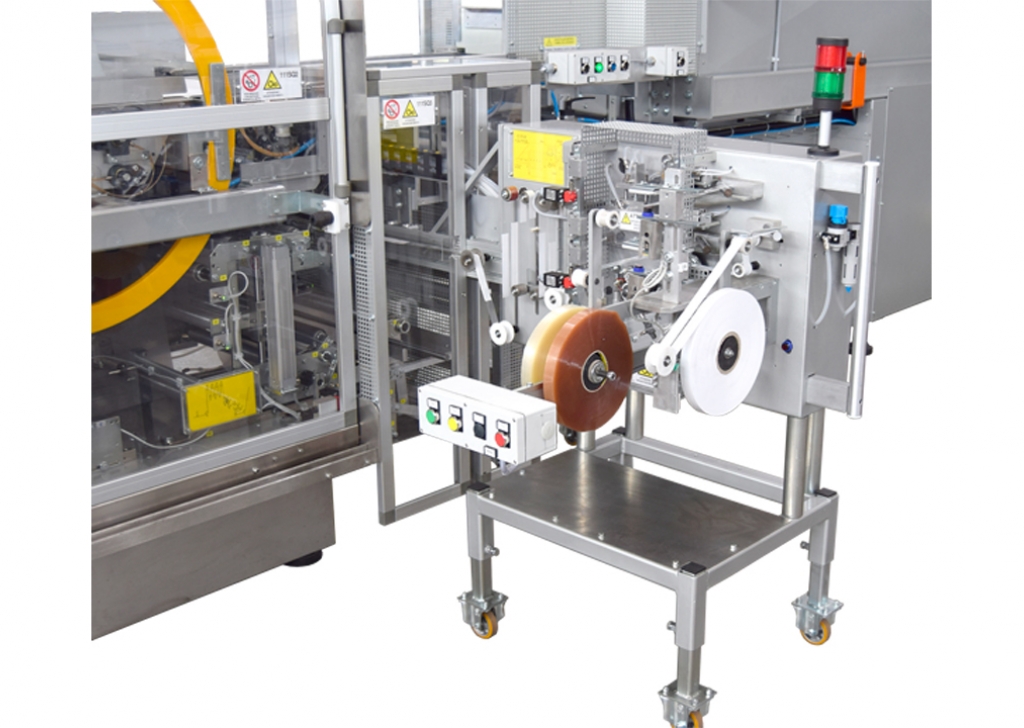
The pre-retraction handle applicator, available in single and double, includes:
- double scotch reel holder (1,500 m) with automatic change or single reel holder (5000 m) paper reel holder (1,500 m)
- paper-scotch coupling and handle cut
- paper length adjustment
- automation and control
- light indicator


Can stacking system consisting of infeed belts complete with overlapping unit with stars.
The cans transported to the entrance of the machine are then packaged in tray + film or wrap-around.
Accessories
On the Zambelli shrink wrappers it is possible to take advantage of an automatic motorized adjustment of the product guides in the areas normally adjustable by means of a handwheel for format change.
All the moving parts of the machine that are subject to format change can be equipped with brushless motors for quick format change.
For easier access by the operator, the reel holder and the manual 90 ° welder are placed on the side of the machine.
In machines that have an automatic welder, in case of use of printed film, a photocell stops the unwinding near the reference notch printed in the film, in order to proceed with the welding between the exhausted reel and the new one.
This system guarantees the perfect position of the printed film without film waste or bundles when restarting after the reel change.
The energy saving bulkheads are present at the entrance and exit of the heat tunnel, designed to lower automatically to reduce energy consumption and to quickly reach the temperature "set point" when the machine is started.
In combination with this, through the PLC it is possible to manage the resistances that turn on and off according to the temperature detected inside the shrink chamber.
Also through the PLC, it is possible to automatically activate the lubrication pump for a time that can be set according to the hours of operation of the machine.
The touch screen PC includes, in addition to what is described, also: the alarm signaling complete with photos and explanation for the relative reset, the video instructions for the format change, the list of recommended spare parts, the wiring diagram, the user manual and maintenance of the machine and, finally, the performance statistics of the machine.
Packaging
Did you know that each machine is available in multiple versions?
We have created intelligent, modular and tailored packaging solutions
to meet every production requirement..